Are you asking the right questions for the digital challenge?
The prevalence of digitally printed product accounts for an increasing amount of sales within todays printing industry. The basic premise of doing away with the expense of physical printing plates, and achieving quicker make ready times for short run work, is an attractive proposition for many printers. But what does this change from mainly conventional to digital print mean in terms of associated business systems, and is this really important anyway?
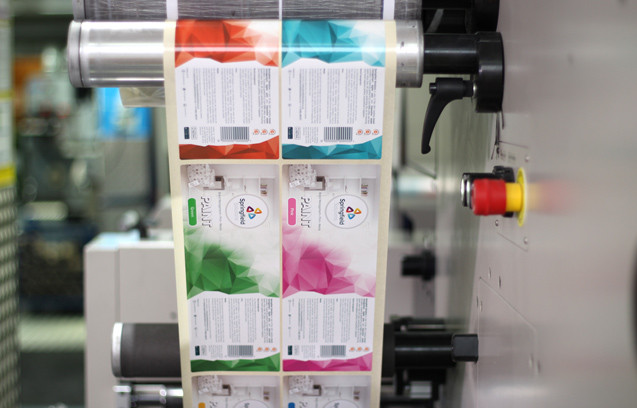
Its fair to say that most of todays digital print technology comes supplied with various state-of-the-art machine controls and ability to communicate with other devices. The term JDF (Job Definition Format) is often bandied around by suppliers of equipment associated with the digital print process to ensure a seamless production route with minimal press adjustment. It could be said however, that similar to a lot of HD TV’s that are advertised as “HD Ready”, it is not usually a case of “Plug and Play” when looking to get devices talking to each other accurately to provide the required data and efficiencies. For many, a greater degree of post installation activity than would be expected is often the norm when looking to optimise the systems associated with digital print equipment.
It is obviously important that any digital label print equipment fulfils its basic function to output quality product quickly and this, quite rightly, should be the primary goal of equipment developers and suppliers. To ensure they get the most out of any equipment purchased, potential purchasers should be mindful in exploring what needs to be done to maximise the process associated with such equipment and other items that are used prior to and after printing. Consideration of what forms the input and output formats that are required for equipment software, as well as any associated MIS system, could be said to be key to optimising the production process.
Thought should also be given to the existing business system’s suitability for any new digital label print equipment. It is often the case that a company’s business systems (ie. ISO 9001, 14001, BRC IoP) have originally been developed for conventional print processes and include traditional tried and trusted quality control methods. The arrival of digital print equipment can sometimes mean that these systems need to be re-evaluated to ensure the use of relevant technology is utilized, whilst maintaining business system compliance.
With shorter runs and quicker make-ready, turnaround times are a key feature and benefit of the digital print process. However, without a degree of business system automation companies can find that it takes longer to carry out the checking of product and the recording of required business information at each stage than it can take to process the work. The use of barcoding systems and scanners as well as appropriately located and specified camera inspection systems are often utilised to reduce the time these activities take. In addition to this, synergy between MIS and digital equipment systems to optimise JDF and prevent double data entry tasks have also been seen to make a positive impact.
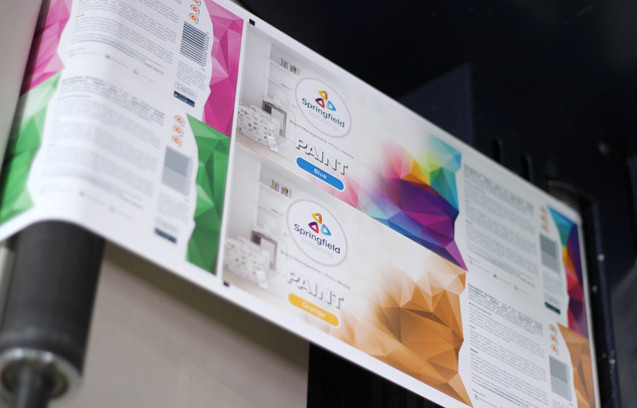
Could it also be said that a key factor here is the mindset of those involved in all aspects of the process? Digital label print equipment has evolved from the conventional print technologies but has the way people think about print identified the importance the associated business system design and implementation in light of a differing digital requirement? To hit the ground running when introducing digital print technology into an existing print business the importance of evaluating existing business systems and ensuring what needs to be done to achieve a seamless production route is as key to early success as the right digital equipment for the product.
If you are considering the leap to digital but have not yet done so, what questions are you going to ask?